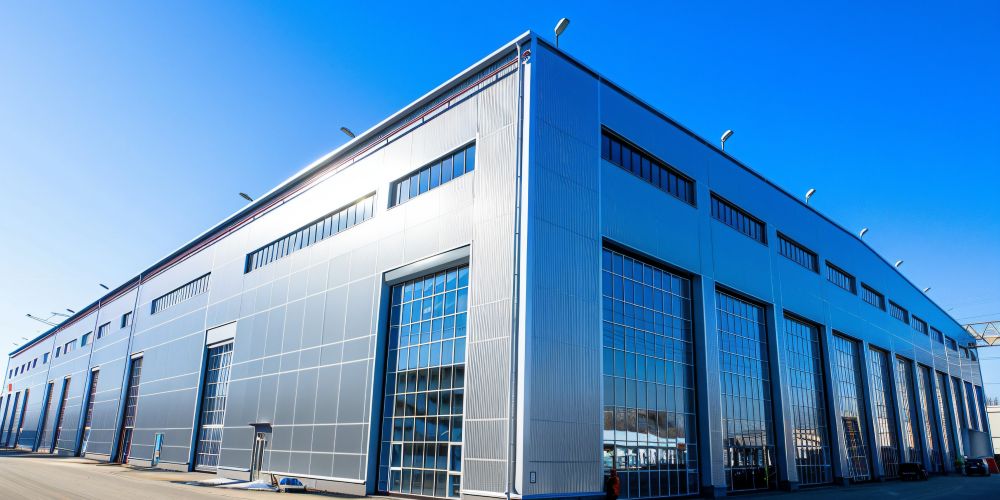
In the context of Saudi Arabia’s economic diversification strategy, steel structure buildings have become the preferred choice for industrial facility construction due to their efficiency, flexibility, and eco-friendliness. Recently, we completed a steel structure industrial plant project for a leading energy company in Saudi Arabia. The plant, measuring 180 meters in length and 60 meters in width, not only met the client’s high requirements for functionality and durability but also solved multiple challenges faced by the client during the project. Below is a detailed account of the project process.
Client Background and Core Needs
The client is a well-known energy company in Saudi Arabia, specializing in the research and development of new energy equipment. With rapid business expansion, the client urgently needed a modern industrial plant to meet growing production demands. The client set the following core requirements for the project:
- Efficient space utilization: The plant needed to accommodate the installation and operation of large equipment while leaving sufficient space for logistics and storage.
- Extreme climate adaptability: Saudi Arabia’s summer temperatures exceed 50°C, and sandstorms are frequent, so the building must withstand high temperatures and sand erosion.
- Fast delivery: The client wanted the project completed in the shortest possible time to quickly resume production.
- Environmental sustainability: The building needed to meet international environmental standards and reflect the client’s commitment to sustainability.
These requirements posed high demands on the design and construction of the project, and our team successfully addressed the client’s challenges with our expertise.
Challenge 1: Efficient Space Layout and Equipment Compatibility
The client needed to install multiple large new energy equipment units inside the plant, while also reserving sufficient logistics and storage space. Maximizing space without compromising equipment operation was a major design challenge.
Our Solution:
- Customized layout design: We worked closely with the client’s technical team to understand the dimensions, operational requirements, and maintenance space for each piece of equipment and tailored the plant’s space layout accordingly.
- Optimized logistics channels: We designed a main logistics channel 8 meters wide and secondary channels 4 meters wide to ensure smooth passage for large transport vehicles and equipment.
- Modular zoning: The plant was divided into production, storage, and logistics areas, each with clear functions and minimal interference, improving overall operational efficiency.
The client highly praised our space layout design, noting that we not only met the equipment installation needs but also greatly enhanced the operational efficiency of the plant.
Challenge 2: Extreme Climate Adaptability
With temperatures exceeding 50°C in the summer and frequent sandstorms, the client was concerned that high temperatures and sandstorms would affect the plant’s lifespan and internal environment.
Our Solution:
- Insulation design: We used high-performance insulation materials for the roof and walls, effectively reducing indoor temperatures and minimizing air conditioning energy consumption. We also designed a double-layer roof structure to further isolate heat using an air layer.
- Sandstorm protection: We added sandstorm barriers around the building and optimized the sealing of doors and windows to prevent sand from entering the interior.
- Corrosion-resistant treatment: We applied a special anti-corrosion coating to all steel surfaces to ensure the building’s longevity in high temperatures and high humidity conditions.
The client was highly impressed with our climate adaptability design, feeling that we truly considered the local environmental conditions and solved their concerns.
Challenge 3: Fast Delivery and Efficient Construction
The client wanted the project completed as quickly as possible to resume production. However, the manufacturing and installation of steel structures typically require a longer period.
Our Solution:
- Modular design and manufacturing: We divided the building into multiple modules, pre-fabricating them in the factory, significantly reducing on-site construction time.
- Parallel construction: While the components were being manufactured in the factory, foundation construction was carried out simultaneously on-site, ensuring that components could be installed as soon as they arrived.
- Efficient logistics and installation: We collaborated with professional logistics companies to ensure safe and fast delivery of components to the site. The installation team used advanced lifting equipment and technology, completing the main structure installation in just 30 days.
The client was very satisfied with our construction efficiency, noting that we maximized the construction speed while ensuring quality.
Challenge 4: Environmental Sustainability
The client wanted the building to reflect the company’s sustainability principles and comply with international environmental standards.
Our Solution:
- Green materials: We selected recyclable eco-friendly steel and strictly controlled carbon emissions during the production process.
- Energy-saving design: We optimized insulation and ventilation designs to reduce energy consumption. We also offered a solar roof option to further lower operating costs.
- Environmental certification: After the project was completed, we assisted the client in applying for international green building certification (e.g., LEED), enhancing their brand image.
The client highly appreciated our environmental design, recognizing that we not only met functional needs but also helped them take an important step towards sustainable development.
Project Results and Client Feedback
This 180×60 meter steel structure industrial plant not only met all the client’s functional requirements but also solved multiple challenges encountered during the project. The project was completed in just 4 months, 20% faster than the client’s expected timeline.
The client highly praised our services: “Your professionalism and efficient execution have left a deep impression on us. Whether it’s the design, construction, or environmental solutions, you exceeded our expectations. This plant not only enhances our production capacity but also serves as a key symbol of our corporate image.”
Conclusion: Professionalism Creating Client Value
Through this project, we once again demonstrated the significant advantages of steel structure buildings in the industrial sector and showcased our professional strength in international projects. Moving forward, we will continue to adhere to the principle of “customer first” and provide high-quality steel structure solutions for clients worldwide, helping them achieve greater business value.